Hydraulic Tube Fittings: Essential Components for Fluid Power Systems
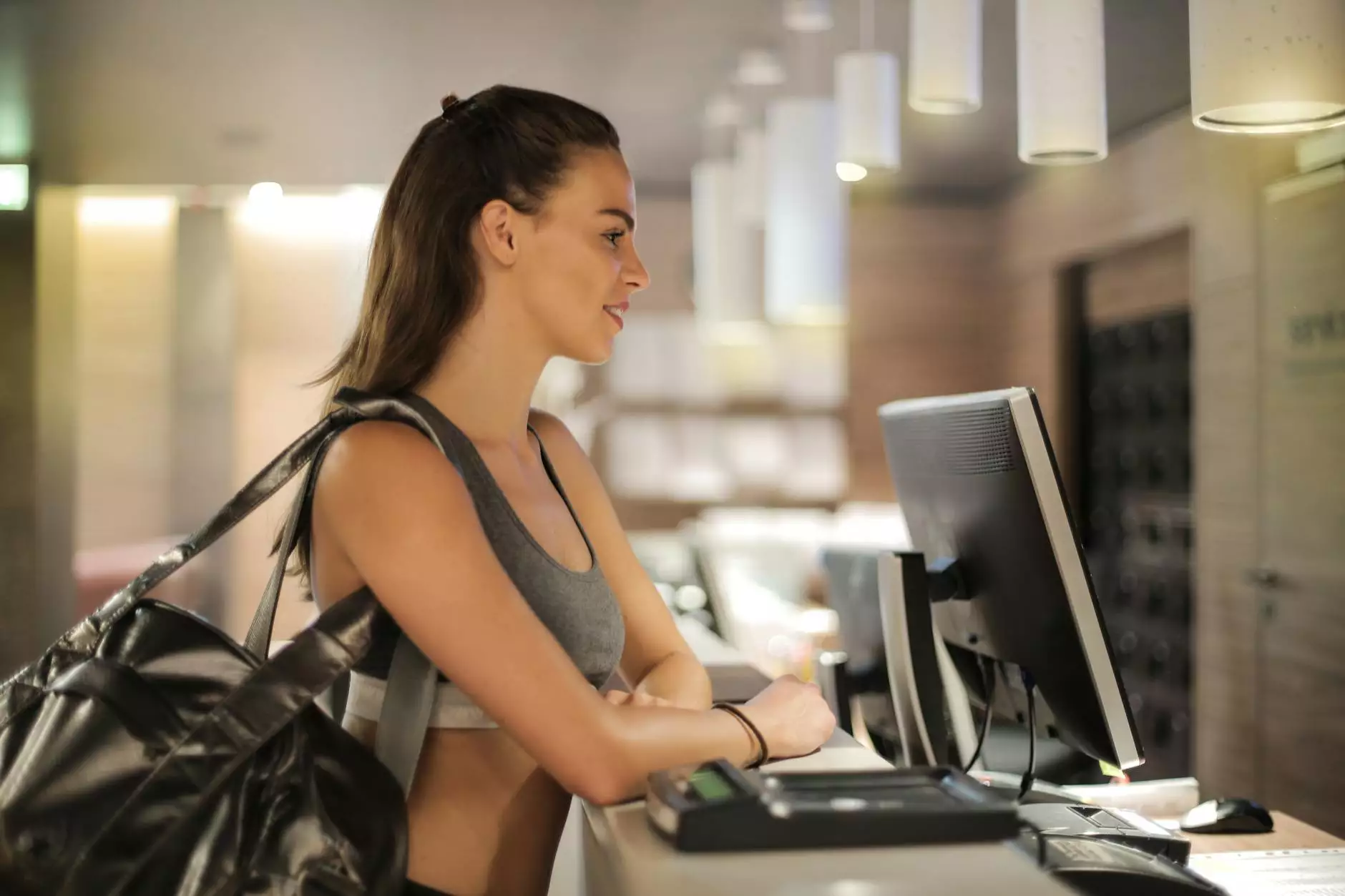
Hydraulic tube fittings are indispensable components in various industrial applications, playing a critical role in the transport and control of hydraulic fluids. Understanding the nuances of hydraulic tube fittings can significantly improve operational efficiency and safety in any hydraulic system. In this article, we will explore the types, applications, benefits, and best practices associated with hydraulic tube fittings, ensuring that you are fully equipped to make informed decisions for your business.
1. Understanding Hydraulic Systems
Before delving into hydraulic tube fittings, it is essential to understand the foundation of hydraulic systems. Hydraulic systems operate on the principle of fluid mechanics, utilizing pressurized fluids to transmit energy and perform work. These systems are widely used in various sectors, including manufacturing, construction, and automotive industries.
2. What Are Hydraulic Tube Fittings?
Hydraulic tube fittings are mechanical components designed to connect hydraulic tubes and hoses in a system. They facilitate the seamless transmission of hydraulic fluids, ensuring that systems operate efficiently and safely. These fittings come in various configurations, materials, and sizes, tailored for specific applications and pressure ratings.
2.1 Types of Hydraulic Tube Fittings
Hydraulic tube fittings are categorized based on their design and function. Here are the most common types:
- Compression Fittings: These fittings create a tight seal when the nut is tightened, compressing the ferrule around the tube.
- Threaded Fittings: Utilizing male and female threads, these fittings are screwed together to secure the connection.
- Welded Fittings: These involve welding the fitting directly to the tube, providing a permanent and robust connection.
- Flanged Fittings: These fittings feature a flat surface with holes for bolting, enabling easy disassembly.
- Quick Disconnect Fittings: Designed for rapid connection and disconnection, these fittings allow for versatile use in mobile applications.
2.2 Materials Used in Hydraulic Tube Fittings
The materials used in manufacturing hydraulic tube fittings are crucial to their performance and longevity. Common materials include:
- Steel: Known for its strength and durability, steel fittings are widely used in high-pressure applications.
- Stainless Steel: Resistant to corrosion, stainless steel fittings are ideal for environments exposed to moisture or chemicals.
- Brass: With good corrosion resistance and machinability, brass fittings are commonly used in various hydraulic applications.
- Aluminum: Lightweight and resistant to corrosion, aluminum fittings are suitable for applications where weight savings are essential.
3. Benefits of Using High-Quality Hydraulic Tube Fittings
Investing in high-quality hydraulic tube fittings offers several advantages that contribute to the efficiency and safety of your hydraulic systems:
- Enhanced Durability: Quality fittings are engineered to withstand high pressure, temperature fluctuations, and corrosive environments.
- Improved Safety: Reliable fittings minimize the risk of leaks and system failures, ensuring safer operations.
- Better Performance: High-quality fittings enable optimal flow characteristics, reducing energy losses and enhancing system efficiency.
- Easier Installation: Well-designed fittings simplify the installation process, saving time and labor costs.
- Cost-Efficiency: While higher upfront costs may occur, investing in quality fittings reduces long-term maintenance and replacement expenses.
4. Applications of Hydraulic Tube Fittings
Hydraulic tube fittings find application across a multitude of sectors. Here are some notable industries where they play a pivotal role:
- Construction: Hydraulics are critical in construction machinery, including excavators, bulldozers, and cranes.
- Aerospace: Hydraulic systems in aircraft rely on highly reliable fittings to manage flight controls and landing gear.
- Automotive: Vehicles use hydraulic systems for braking, steering, and suspension, all requiring robust fittings.
- Manufacturing: Machinery and automation systems in factories utilize hydraulic power, demanding high-performance fittings.
- Marine: Ships and offshore equipment use hydraulic systems for propulsion and control, heavily relying on quality fittings.
5. Factors to Consider When Choosing Hydraulic Tube Fittings
Selecting the right hydraulic tube fittings for your application involves several critical considerations:
5.1 Pressure Rating
Understanding the pressure requirements of your hydraulic system is essential. Always choose fittings that exceed the maximum pressure of your application.
5.2 Size and Compatibility
Ensure that the fittings match the diameter and type of tubing being used. Compatibility is key to achieving a secure connection.
5.3 Material Selection
Choose materials that resist the environment in which they will operate, considering factors like temperature, pressure, and exposure to chemicals.
5.4 Installation and Maintenance
Consider ease of installation and if regular maintenance is required. Some fittings may need frequent inspections and replacements.
6. Best Practices for Installing Hydraulic Tube Fittings
Proper installation of hydraulic tube fittings is crucial for ensuring system performance and longevity. Here are some best practices to follow:
- Inspect Components: Always check the fittings, tubes, and seals for damage or wear before installation.
- Follow Manufacturer Guidelines: Use the manufacturer's instructions to ensure correct torque settings and installation procedures.
- Deburr Tubes: Ensure the ends of the tubes are deburred to avoid scratching or damaging seals.
- Use Proper Tools: Employ appropriate tools for installation to prevent cross-threading and other installation errors.
- Leak Testing: After installation, perform a leak test to ensure the integrity of the connections.
7. Conclusion
In conclusion, hydraulic tube fittings are critical components that ensure the efficacy and safety of hydraulic systems. By understanding their types, benefits, and best practices for selection and installation, businesses can enhance their operational efficiencies. For those looking to purchase high-quality hydraulic fittings, consider exploring the offerings at fitsch.cn, where quality meets reliability.
Investing in the right hydraulic tube fittings is not just a matter of convenience; it is a decision that impacts the performance and safety of your hydraulic systems and, ultimately, your business success.