The Transformative Role of Plastic Injection Molders in Electronics and Medical Supplies
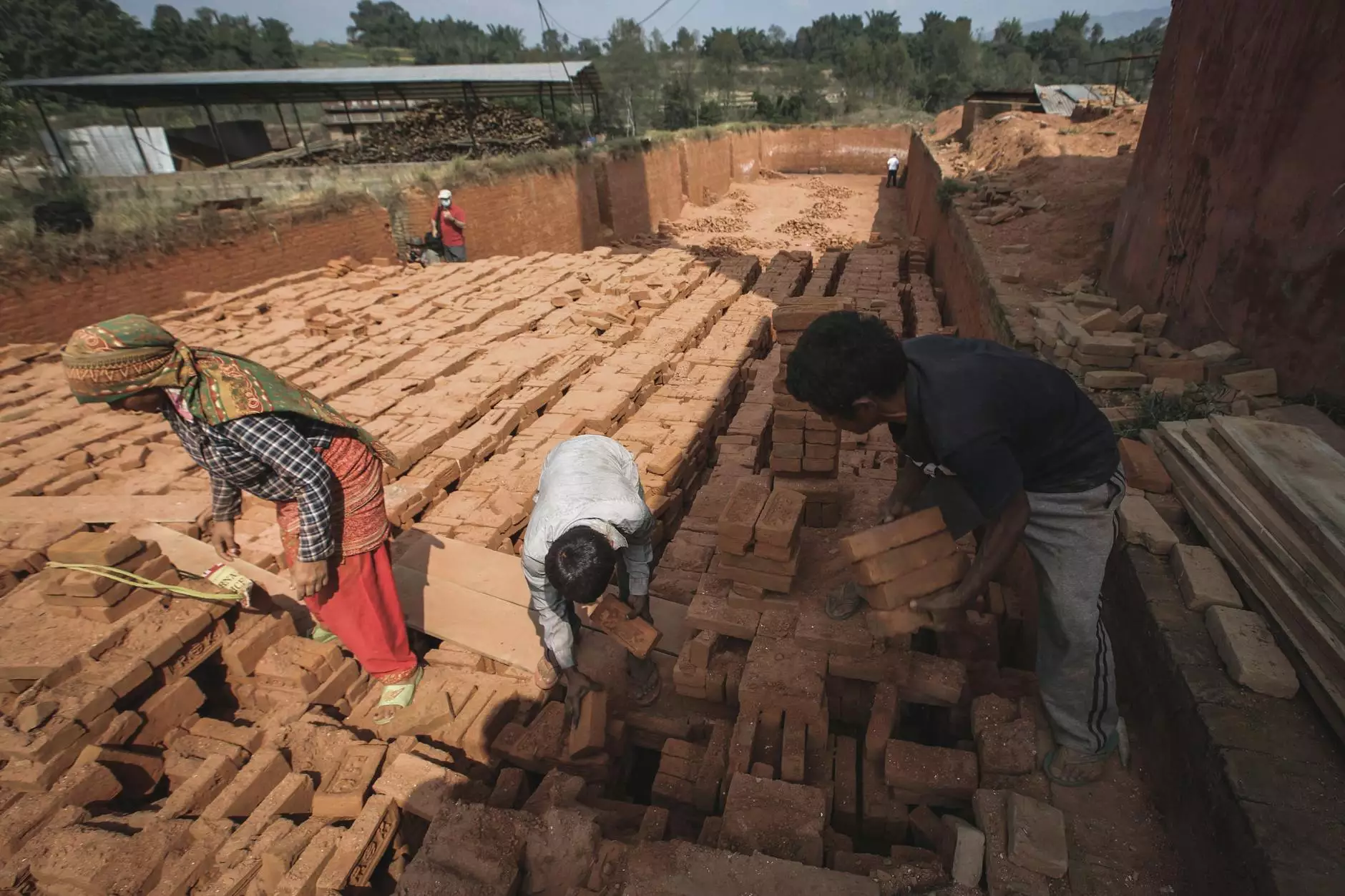
Understanding Plastic Injection Molding
Plastic injection molding is a crucial manufacturing process that involves the production of plastic parts by injecting molten material into a mold. The process is known for its ability to create highly precise and complex shapes while ensuring efficiency and scalability. Industries such as electronics and medical supplies have embraced this innovative technology for the many advantages it offers.
Why Choose Plastic Injection Molding?
There are several reasons why businesses in the electronics and medical sectors prefer plastic injection molders:
- Cost-Effectiveness: Once the mold is created, producing parts doesn’t require significant additional investment, leading to lower per-unit costs with higher production volumes.
- Speed: The process allows for rapid production cycles, drastically reducing time to market.
- Material Versatility: Various thermoplastics and thermosets can be utilized, enabling custom solutions for different applications.
- High Precision: Injection molding provides excellent tolerances and repeatability, making it ideal for intricate designs, especially in electronics.
- Reduced Waste: The process is highly efficient, producing minimal waste compared to traditional manufacturing methods.
Applications of Plastic Injection Molders in Electronics
The electronics industry demands high performance and reliability, both of which are met through the use of plastic injection molders. Here are some key applications:
1. Consumer Electronics
In consumer electronics, components such as smartphone casings, remote controls, and computer parts often undergo injection molding. The accuracy of plastic molding allows for intricate designs that can include electronic circuitry or battery housing.
2. Electrical Connectors and Enclosures
Electrical connectors are essential for functionality in most electronic devices. Molding ensures that connectors are built to meet rigorous standards while also offering customization to cater to specific connectivity needs.
3. Circuit Boards
Injection molding is used to create housings and casings for circuit boards, protecting them from environmental factors while allowing for easy access and interconnectivity.
Applications of Plastic Injection Molders in Medical Supplies
The medical industry relies on plastic injection molders for the production of components that require stringent quality and regulatory compliance. Some applications include:
1. Surgical Instruments
Surgical instruments must be precise and durable. Injection molding allows for the mass production of these tools with high standards of sterility and accuracy.
2. Disposable Medical Supplies
Items such as syringes, IV bags, and other disposable medical supplies are produced using injection molding technology. This ensures that the products meet hygiene standards while being cost-effective.
3. Diagnostic Equipment
Devices used in diagnostics often require various components that need to be light, durable, and precise. Injection molding facilitates the production of these components to exact specifications.
Innovations in Plastic Injection Molding Technology
As industries evolve, so do the technologies surrounding plastic injection molders. Innovations in this field are helping companies stay ahead of the curve:
1. Advanced Materials
New polymer materials with enhanced properties are allowing for greater flexibility and durability in plastic parts. Innovations in bioplastics are paving the way for more sustainable manufacturing practices.
2. Automation and Robotics
Integration of automation and robotics into the injection molding process has increased efficiency and precision, reducing human error, and allowing for continuous, unattended production runs.
3. Simulation Software
Advanced simulation software now enables manufacturers to model the injection process before production. This leads to better design decisions, reduced waste, and minimized costs.
Choosing the Right Partner for Plastic Injection Molding
When selecting a plastic injection molder, companies should consider several factors:
1. Experience and Expertise
Look for a partner with proven experience in both the electronics and medical sectors. They should understand industry-specific requirements and compliance standards.
2. Quality Control Processes
Ensure that the manufacturer has robust quality control processes in place, including inspection and testing protocols to guarantee that all parts meet the necessary specifications.
3. Capacity and Scalability
An ideal partner should have the capacity to handle both small and large production runs and the ability to scale up operations as your demand grows.
The Future of Plastic Injection Molding
The landscape of plastic injection molders continues to evolve with emerging technologies and market demands. Businesses are moving towards more sustainable practices, pushing for innovations that reduce environmental impact. The future will likely see:
1. Enhanced Sustainability
As industries respond to environmental concerns, recycling and the use of environmentally friendly materials will become integral to injection molding.
2. Customization Trends
As consumers demand more personalized products, the ability to offer custom, low-volume production runs through injection molding will increase in importance.
3. Globalization and Supply Chain Efficiency
With globalization, businesses will seek partners that can offer competitive, efficient solutions, enabling streamlined operations that can adapt to shifting market demands.
Conclusion
In summation, plastic injection molders play an invaluable role in advancing the electronics and medical supplies industries. The combination of efficiency, cost-effectiveness, and precision positions them as a pivotal technology for modern manufacturing. As the landscape continues to change, staying informed about innovations and trends in this field will be crucial for businesses looking to maintain a competitive edge.