Unveiling the Power of Ultem 1010: A Journey through Innovation
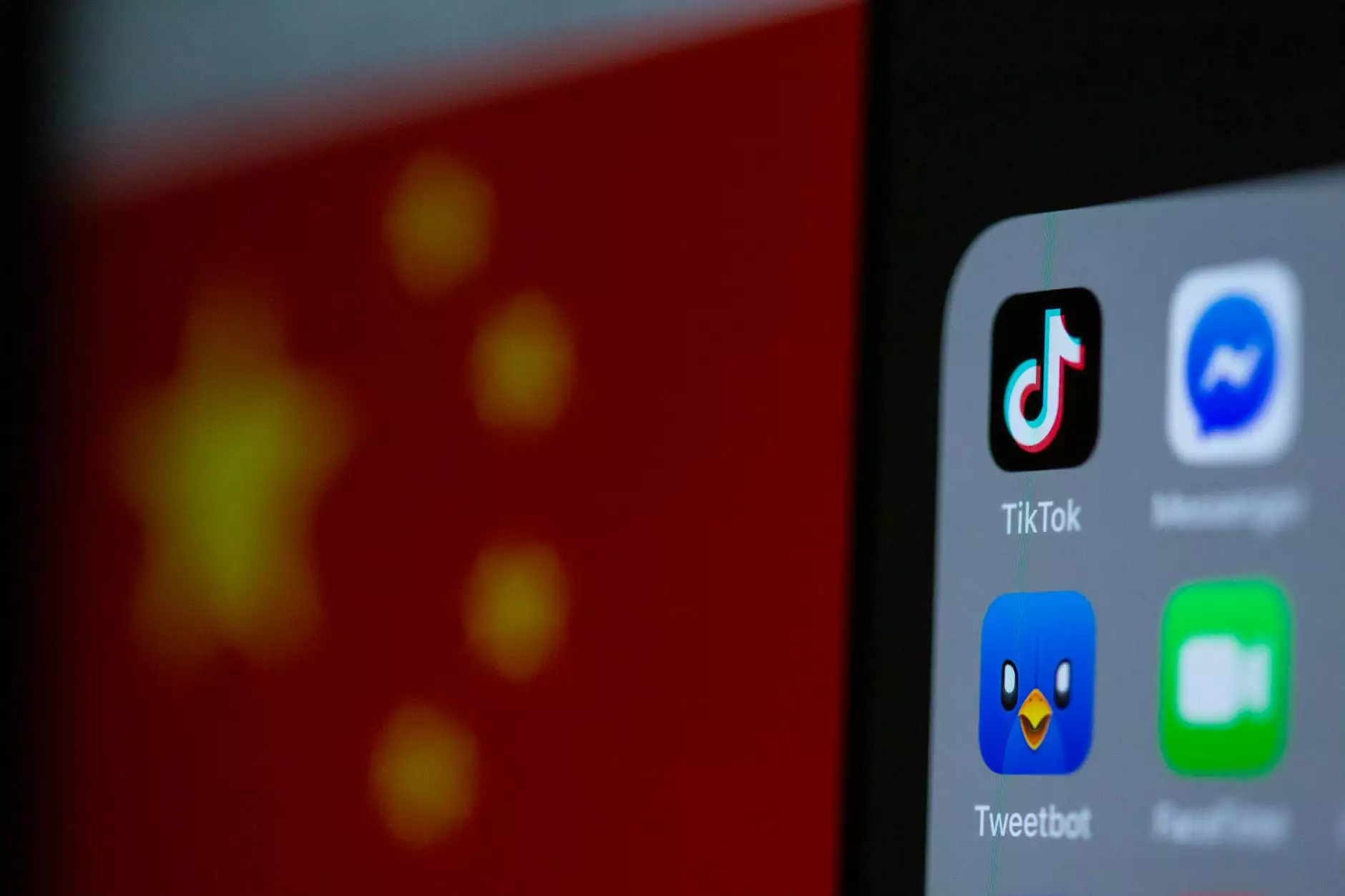
In today's fast-paced industrial environment, the selection of materials plays a crucial role in the development of advanced products. One such material that has captured the attention of engineers, designers, and manufacturers alike is Ultem 1010. This high-performance thermoplastic is renowned for its exceptional strength, thermal stability, and chemical resistance, making it an ideal choice for various applications across multiple industries.
The Composition and Properties of Ultem 1010
Ultem 1010, a polyetherimide (PEI) resin, is characterized by its unique molecular structure, which imparts remarkable properties that set it apart from conventional plastics. Some of its defining characteristics include:
- High Heat Resistance: Ultem 1010 maintains its integrity and mechanical properties at elevated temperatures, with a glass transition temperature of approximately 217°C (423°F).
- Excellent Chemical Resistance: It withstands exposure to various chemicals, including acids and bases, making it suitable for demanding environments.
- Superior Mechanical Strength: The material exhibits high tensile strength and rigidity, ensuring durability in applications requiring structural integrity.
- Electrical Insulation: Ultem 1010 provides excellent electrical insulation, making it a favored choice in electronic components.
Applications of Ultem 1010 in Various Industries
Thanks to its versatility, Ultem 1010 is used in a broad range of industries, including aerospace, automotive, medical, and consumer products. Below are some notable applications:
1. Aerospace Industry
In the aerospace field, where weight reduction and performance are critical, Ultem 1010 is increasingly used for:
- Interior Components: Used in aircraft interiors for its aesthetic qualities and compliance with stringent safety standards.
- Electrical Insulation: The material serves as an insulating substrate in electrical connectors and components.
- Structural Parts: Its strength allows for lightweight yet durable structural components.
2. Automotive Applications
For automotive manufacturers, Ultem 1010 offers the following advantages:
- High-Temperature Performance: Ideal for parts exposed to high temperatures, such as engine components and exhaust systems.
- Weight Reduction: Ultem's lightweight nature contributes to improved fuel efficiency.
- Durability: Resistant to a variety of oils and fluids present in automotive environments.
3. Medical Devices
In the medical sector, where sterility and reliability are paramount, Ultem 1010 is utilized for:
- Surgical Instruments: Its strength and biocompatibility make it suitable for precision surgical instruments.
- Drug Delivery Systems: Employed in components that require high chemical resistance and stability.
- Diagnostic Equipment: Used in the manufacturing of diagnostic devices where durable and non-toxic materials are essential.
4. Consumer Products
Ultem 1010 also finds its way into everyday consumer products, enhancing their functionality:
- Household Appliances: Components in high-temperature appliances benefit from Ultem's thermal stability.
- Electronic Devices: Used in casings and components where electrical insulation is crucial.
- Art Supplies: In the realm of art supplies, Ultem holds potential for applications in tools and instruments that require durability and precision.
Ultem 1010 in Product Design and 3D Printing
The advent of 3D printing technology has expanded the possibilities for utilizing Ultem 1010. This material, especially in filament form, is becoming increasingly popular among product designers and innovators. Here’s how:
1. Fused Deposition Modeling (FDM)
Ultem 1010 is suitable for FDM 3D printing, making it accessible for rapid prototyping and small-scale production. Designers can create intricate geometries and complex parts that would be difficult to achieve with traditional manufacturing methods.
2. Enhanced Performance Parts
For applications requiring high performance, Ultem 1010 can be 3D printed to produce parts that can endure extreme conditions. This opens new avenues in sectors like aerospace and automotive, where prototypes can be tested without the need for expensive molding processes.
3. Customization and Iteration
The flexibility offered by 3D printing allows designers to iterate quickly. With Ultem 1010, changes in design can be made and tested without significant downtime, promoting innovation and efficiency in the product development cycle.
Why Choose Ultem 1010 for Your Next Project?
When considering a material for your next project, Ultem 1010 stands out for various compelling reasons:
- Long-Term Cost Efficiency: While the initial investment may be higher, the longevity and durability of Ultem 1010 lead to lower lifecycle costs.
- Regulatory Compliance: Ultem 1010 meets numerous industry standards, making it compliant for sensitive applications, especially in the medical and aerospace fields.
- Innovation Potential: Its unique properties and compatibility with 3D printing allow designers to think outside the box and develop cutting-edge products.
Conclusion: Embrace the Future with Ultem 1010
As industries continue to evolve and demand high-performance materials, the relevance of Ultem 1010 is undeniable. From aerospace to consumer products, its versatility and exceptional properties make it a preferred choice for product designers and manufacturers looking to innovate and excel. With Ultem 1010, the possibilities are limitless—so why not consider it for your next groundbreaking project? At arti90.com, we understand the unique requirements of different industries and are ready to assist you in selecting the right materials to bring your ideas to life.