Understanding Plastic Injection Molds: A Comprehensive Guide
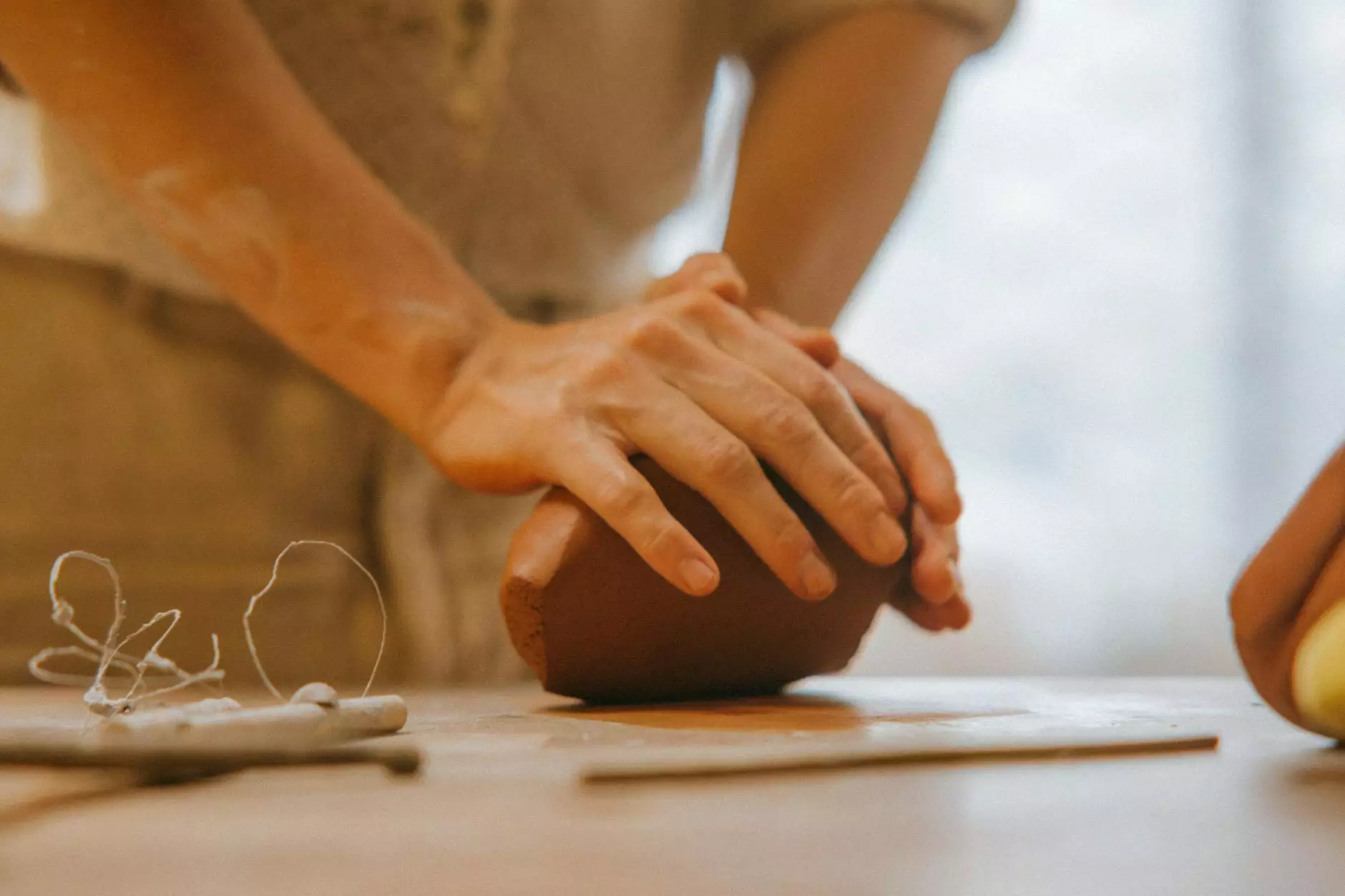
In today’s fast-paced world of manufacturing, the significance of plastic injection molds cannot be overstated. They serve as the backbone for producing high-quality plastic components across various industries, including automotive, consumer goods, and medical devices. This article will delve deep into the intricacies of plastic injection molds, elaborating on their manufacturing processes, benefits, applications, and critical considerations for businesses looking to thrive in this sector.
What are Plastic Injection Molds?
Plastic injection molds are precision-engineered tools used to create plastic parts through a process known as injection molding. The process involves heating plastic material until it becomes a molten liquid, which is then injected into a mold cavity. Once cooled, the plastic hardens into the desired part shape. This method offers unparalleled accuracy and efficiency, making it a preferred choice for mass production.
The Plastic Injection Molding Process
The process of creating plastic components through injection molding can be broken down into several key steps:
- Material Preparation: The first step involves selecting and preparing the plastic material, usually in the form of small pellets. Common materials include ABS, PVC, and polypropylene.
- Melting: The plastic pellets are fed into a hopper and heated in a barrel. As the temperature rises, the pellets melt into a viscous liquid.
- Injection: The molten plastic is injected under high pressure into a mold cavity through a nozzle.
- Cooling: Once injected, the molten plastic takes the shape of the mold as it cools and solidifies.
- Demolding: After sufficient cooling time, the mold opens, and the finished part is ejected.
- Finishing: The component may undergo secondary operations, such as trimming or assembly, to achieve the final product specifications.
Advantages of Plastic Injection Molds
Utilizing plastic injection molds in manufacturing offers numerous advantages:
- High Efficiency: Injection molding is a rapid process that allows for bulk production of parts with minimal waste.
- Cost-Effective: Once the mold is created, the cost per unit decreases significantly, making it ideal for large production runs.
- Precision Manufacturing: Injection molds can produce parts with tight tolerances and intricate designs that are difficult to achieve with other methods.
- Versatility: A wide range of materials can be used, allowing manufacturers to create diverse products that meet specific needs.
- Minimal Post-Processing: Parts typically require little to no finishing work after removal from the mold, reducing labor costs.
Applications of Plastic Injection Molds
Plastic injection molds find applications in a multitude of industries, showcasing their versatility and adaptability:
1. Automotive Industry
The automotive sector heavily relies on plastic injection molds for creating components such as dashboards, bumpers, and interior trim parts. The lightweight nature of plastic contributes to fuel efficiency while maintaining safety standards.
2. Consumer Goods
From toys to kitchenware, consumer products benefit from injection molding. Companies can produce aesthetically pleasing and ergonomic designs that appeal to consumers.
3. Medical Devices
In the medical field, precision and hygiene are paramount. Plastic injection molds facilitate the production of components like syringes, IV bags, and other critical medical devices while ensuring compliance with safety regulations.
4. Electronics
Injection molding supplies the electronics industry with casing for gadgets, connectors, and other intricate parts that require both durability and visual appeal.
Choosing the Right Injection Molding Service
When considering plastic injection molds for your business, it's vital to choose a reputable manufacturer that aligns with your production goals. Here are some factors to consider:
- Experience and Expertise: Look for a manufacturer with a proven track record in specific industries relevant to your business.
- Quality Assurance: Ensure they follow stringent quality control processes to deliver consistent and reliable products.
- Flexibility: A good injection molding partner will be able to accommodate varying production runs, adapting as necessary to your changing needs.
- Technology: Utilizing the latest technologies in design and production can enhance the quality and efficiency of the molds.
- Cost-and-Value Proposition: While cost is a factor, consider the overall value, including lead times, customer service, and technical support.
Design Considerations for Plastic Injection Molds
Effective mold design is pivotal for successful injection molding. Here are key considerations to keep in mind:
1. Part Geometry
Designing for manufacturability (DFM) ensures that your part's geometry allows for easy molding. Avoid sharp corners and deep recesses which can complicate the injection process.
2. Material Selection
Choose a suitable resin that meets the mechanical and aesthetic requirements of the end product. Consider factors such as temperature resistance, strength, and flexibility.
3. Mold Structure
The mold's structural integrity is critical. Utilize advanced engineering to ensure the mold can withstand the pressures of the injection process while maintaining longevity.
4. Gate Design
The gate is the point where plastic enters the mold. Selecting the right gate type and location is essential for controlling flow and minimizing defects.
The Future of Plastic Injection Molding
As industries evolve and sustainability becomes a priority, the future of plastic injection molds is set to transform significantly. Innovations are emerging in biodegradable materials and advanced 3D printing technologies that integrate with traditional molding methods.
1. Sustainability
Companies are increasingly exploring sustainable materials that reduce environmental impact. This shift requires mold designs that accommodate new material behaviors, promoting eco-friendly practices without sacrificing quality.
2. Automation and Smart Manufacturing
The integration of automation in the injection molding process is streamlining production, reducing lead times, and increasing accuracy. Smart technologies allow real-time monitoring and adjustments to enhance efficiency.
Conclusion
The role of plastic injection molds in modern manufacturing is critical. They provide a cost-effective, efficient, and versatile means of producing high-quality plastic components in various applications. As technology advances and market demands shift, staying informed about the latest trends and innovations in plastic injection molding will be essential for businesses aiming to stay competitive.
Investing in quality plastic injection molds and choosing the right partner can significantly impact your operational efficiency, product quality, and ultimately, your bottom line. Explore the opportunities that plastic injection molds offer and leverage them for your business success.
For further assistance on how to leverage plastic injection molds for your business, visit deepmould.net.